- Home
- Adaptive Torque System Specifiers
ENSURE YOUR DESIGN SPECIFICATIONS ARE IMPLEMENTED ON SITE
Specifying Hilti’s HST3 expansion anchors along with our intelligent, cordless impact wrench means installed as designed
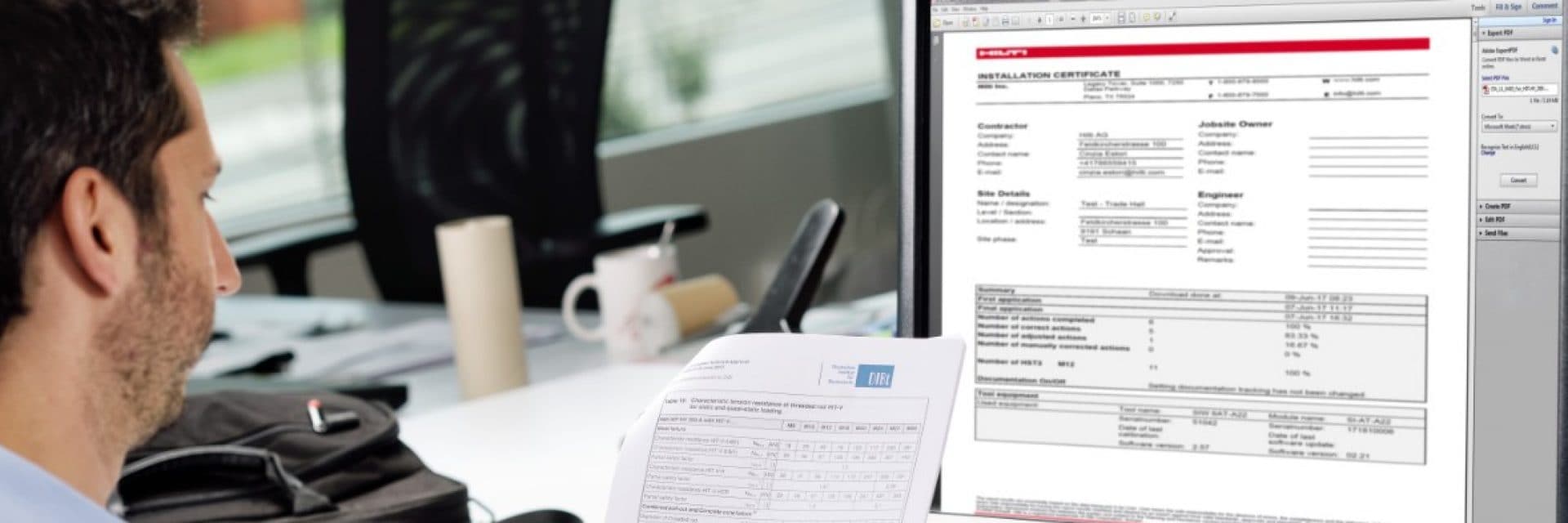
Torque: hard to see; easy to neglect. When it comes to anchoring in concrete, applying the right torque is critically important. Put bluntly, if an anchor is not set with the specified torque, it is only a matter of time before defects creep in. In fact, the American Construction Inspector Association (ACIA) ranks over-and under-torqued anchors as the number-two reason for failed jobsite inspections.
There are many reasons for why the specified torque would not make it all the way from the instruction for use to reality. Foremost among them is speed: with scheduling pressure constantly increasing, finding the time to carefully set and check every single anchor is practically impossible. On top of that, experienced jobsite professionals with the necessary specialized training are not always on hand.
What are consequences of incorrect torquing?
ORDER NOW
-
HILTI COUNTER Intelligent cordless impact wrench for installation of torque-controlled metal expansion anchors -
HILTI COUNTER Lightweight interface module used to generate installation data and reports. -
HILTI COUNTER Our highest performing wedge expansion anchor for bearing high static and seismic loads in cracked concrete (carbon steel).
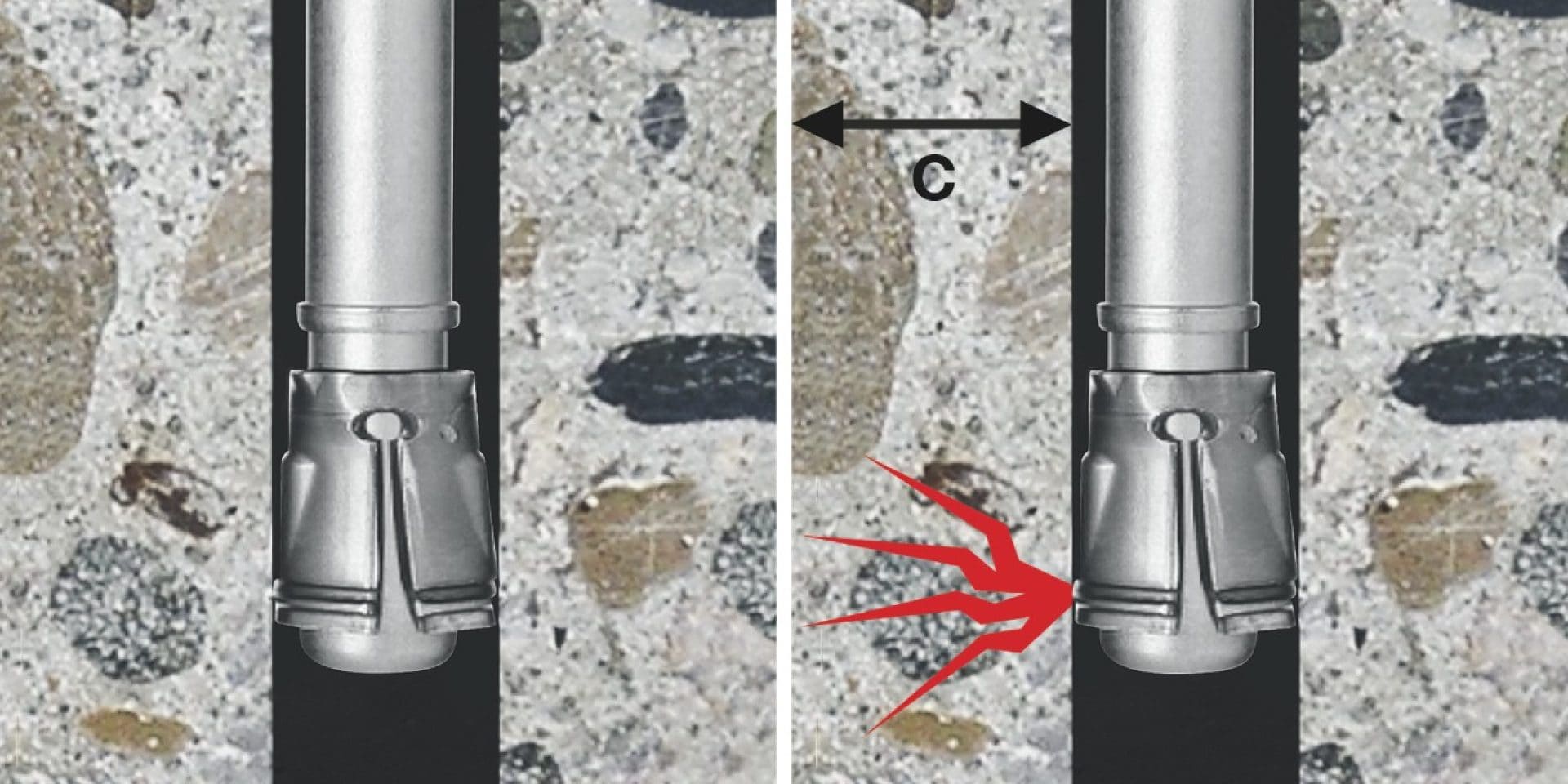
The different between a correctly torqued anchor and an anchor which has been over torqued near to an edge.
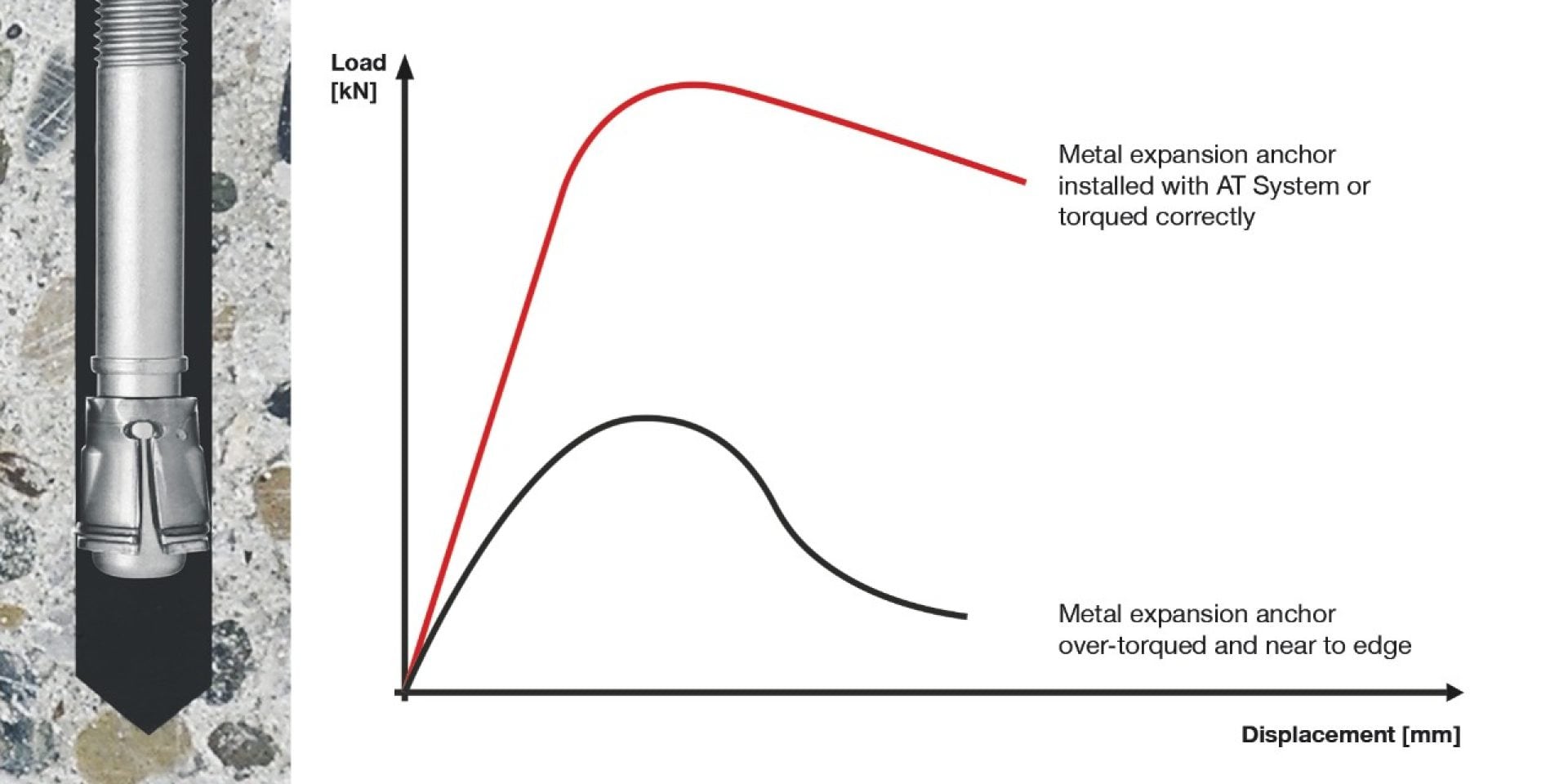
An anchor over-torqued away from the edge results in the cone being pulled too far into expansion sleeve, generating high splitting forces.
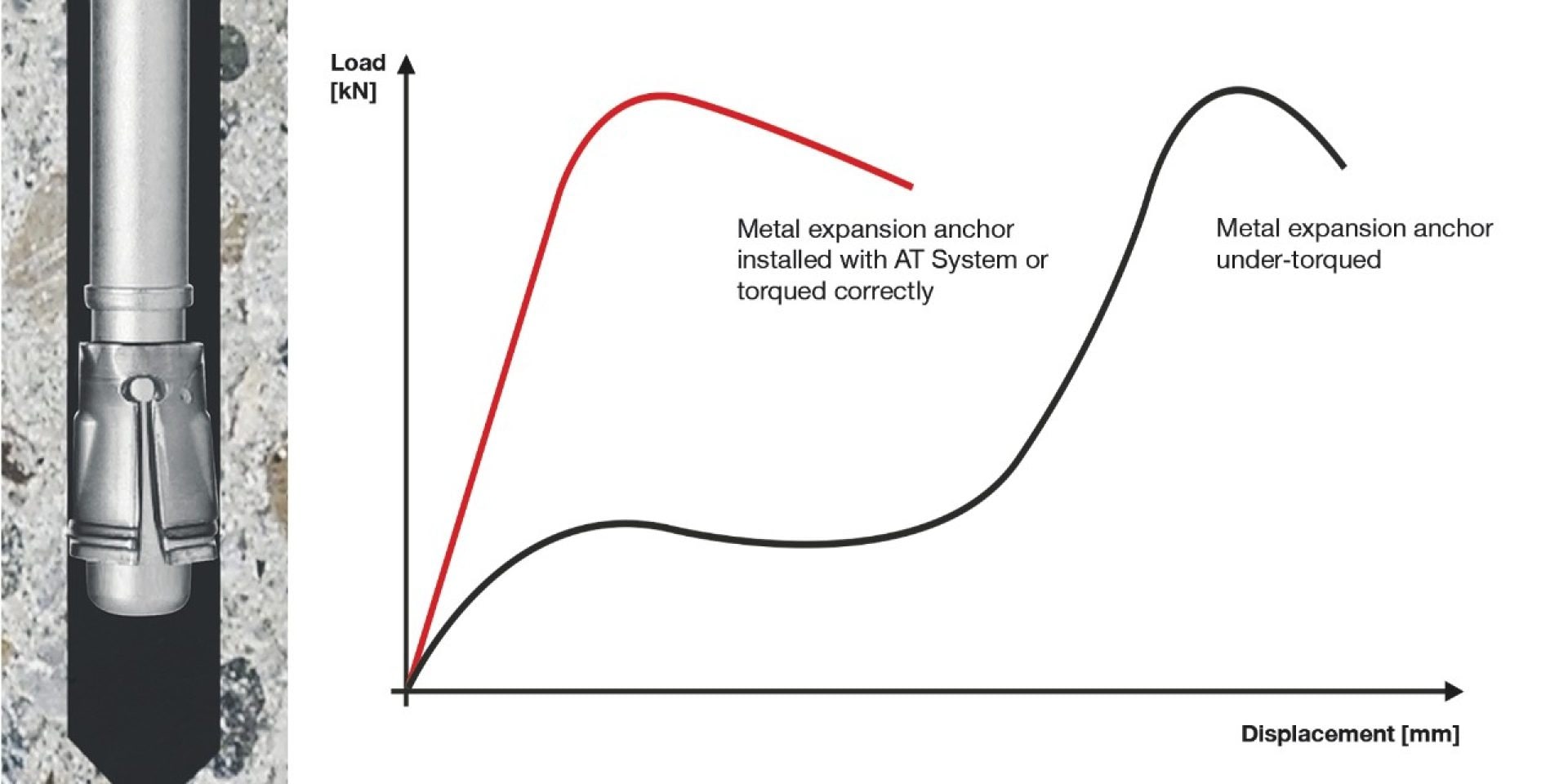
An under-torqued anchor results in the cone being in the incorrect position i.e. it is not drawn far enough into the expansion sleeve, to achieve the specified holding values.
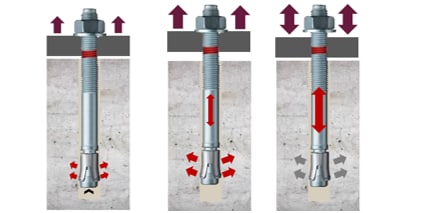
Understanding the dangers of over-torqueing
Over-torqueing results in the cone being pulled too far into expansion sleeve. This generates high forces during setting which may be powerful enough to cause spalling at the slab edge (when concrete splits or breaks away in chips), reducing the load carrying capacity of the base material.
The biggest problem with spalling is that it is not always visible to the naked eye. But even when visible and promptly remediable, the reparation can prove labor-intensive to fix, as new fastening points should be found and the steel must be adjusted accordingly. Much worse is when the spalling cannot be seen. This occurs often when it is hidden under a steel plate, for example, and therefore the flaw remains undetected and unrepaired.
With AT-ready tools and the HST3 anchors, you can significantly reduce the risk of structural defects caused by improper torque.
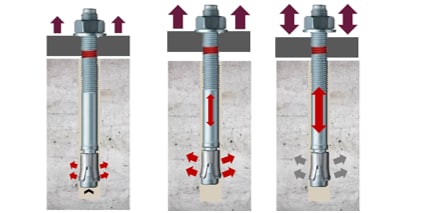
Understanding the dangers of pre-damage
Over-torqueing an anchor always results in the cone being pulled too far into expansion sleeve, generating high splitting forces. However, when the anchor sits far from the slab edge, the splitting forces can be absorbed by the surrounding concrete without any damage.
If the anchor is significantly over-torqued, then the steel bolt can be damaged – or even broken apart – by this torsional moment. The result is a clear drop of the steel failure load under tension, shear, or combined tension and shear forces, up to the point of breakage. As with spalling, the biggest problem with anchor damage is that it can easily go undetected. As a visual inspection of a set anchor is impossible, pre-damage can generally only be detected by a polish-cut image of a cross section. Applying torque in order to gauge the condition of the anchor could worsen any existing damage.
Specifying the adaptive torque system from Hilti is your best method of protecting compatible anchors from unseen damage.
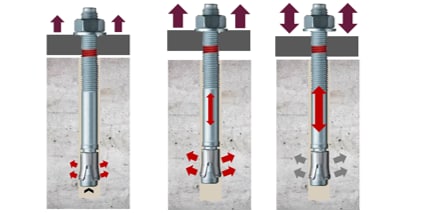
Understanding the dangers of under-torqueing
An under-torqued anchor can be just as problematic as an over-torqued one. Under-torqueing results in the cone being in the incorrect position i.e. it is not drawn far enough into the expansion sleeve to achieve the specified holding values.
Only once the external load is applied does the anchor shift and the cone get pulled in the right direction. In other words, the anchor was loose and relied on external loading to set it rigidly into place. The maximum load or resistance values can be achieved, but only once the anchor has been pulled slightly from the intended position. The result is an installation with unforeseen displacement, as illustrated.
Loose anchors are extremely easy to avoid when using an AT-ready impact wrench.
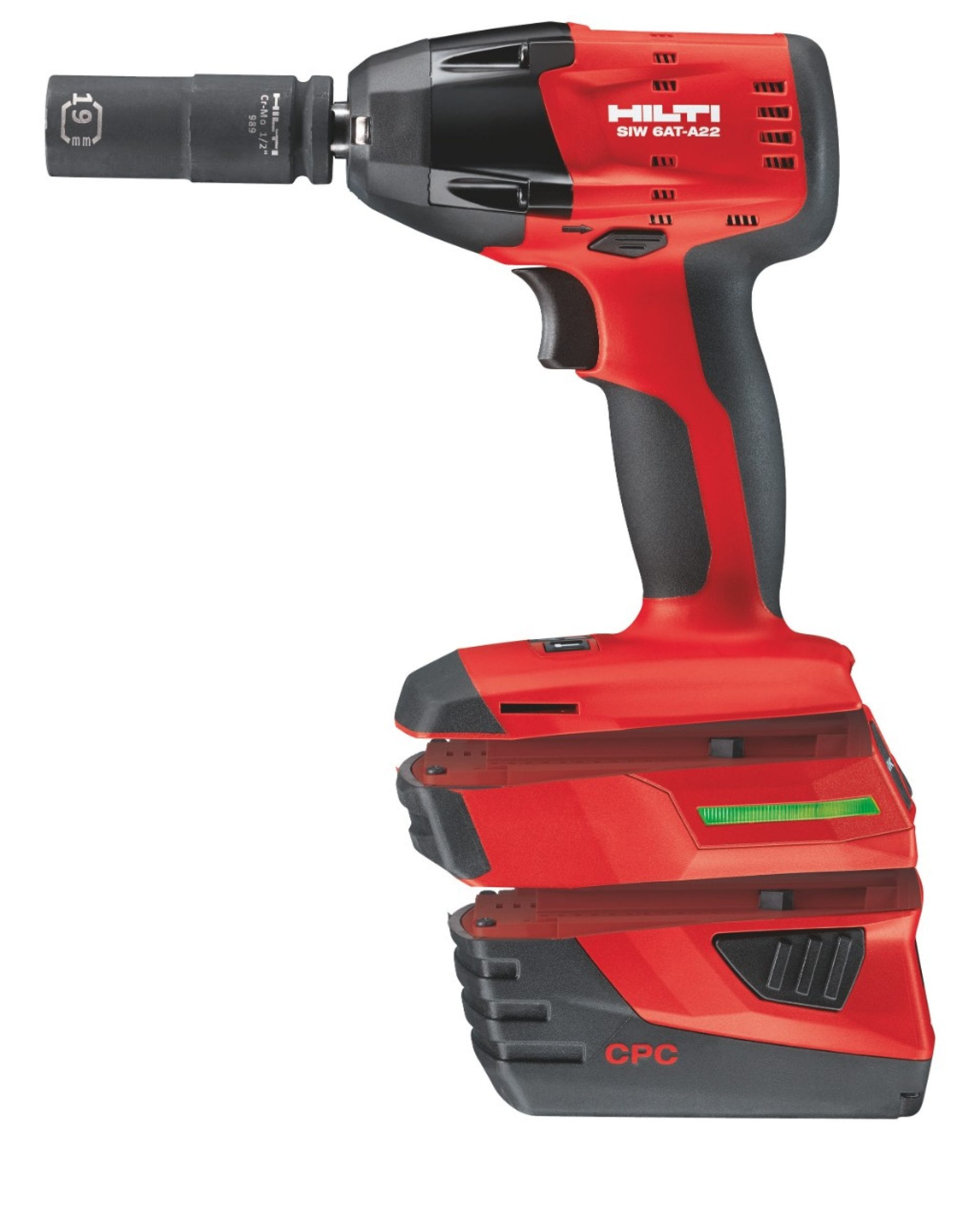
The AT system is made up of four components:
- Hilti HST2 and HST3 expansion anchors (in M8, M10 and M12 diameters), probably the most-specified anchors in the world.
- SIW 6AT-A22 cordless impact wrench with intelligent electronics.
- SI-AT-A22 data processing module which slides in between the impact wrench and its battery. This number-cruncher processes data from sensors within the impact wrench to confirm that the nut is being hit with the right torque for the right amount of time.
- Documentation software so that the main job history of the HST2 and HST3 installation can be transferred from the SI-AT-A22 processor module to a computer. This raw data is used to create a detailed installation certificate.
Hilti AT-ready tools are equipped with the on-board intelligence to confirm if an anchor has been torqued to meet ETA and ICC-ESR approvals. At any time, the SI-AT-A22 can be connected to a computer to instantly generate an installation report, providing inspectors and specifiers with a guarantee that the anchor was set according to the instructions for use.
WHAT ARE THE BENEFITS OF THE ADAPTIVE TORQUE SYSTEM
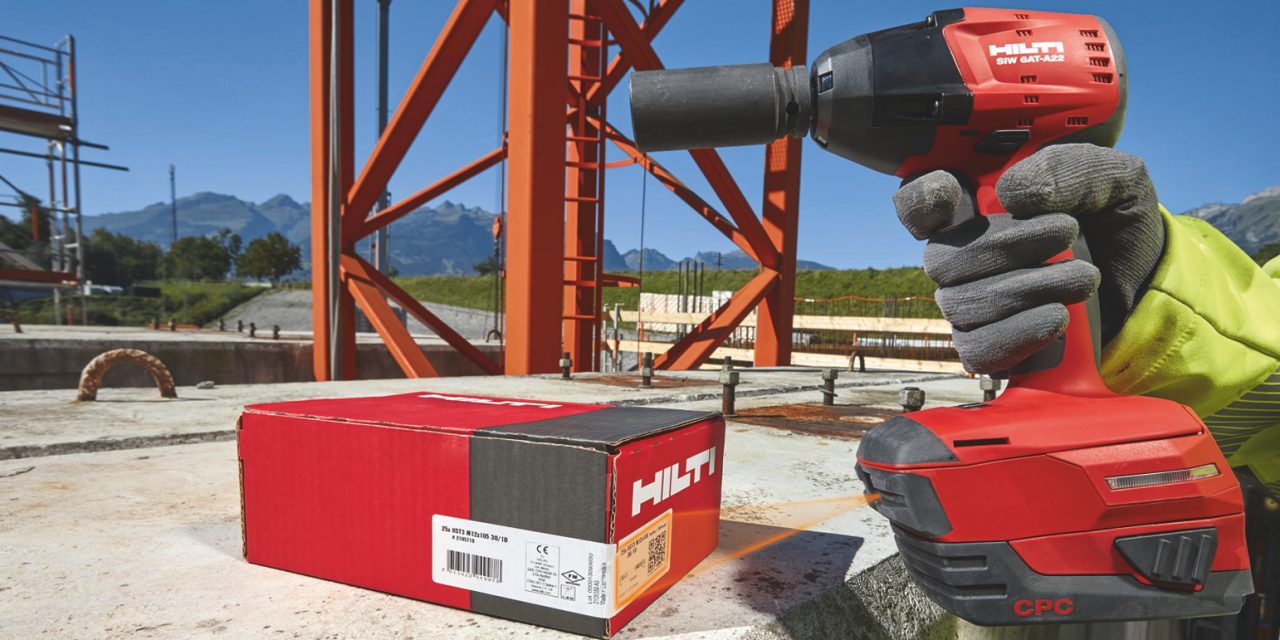
Design and Specification
The AT System gives you certainty that design specifications will be fully implemented on site.
No need to 'design in' additional safety factors to compensate for anchors which are underperforming due to incorrect torque.
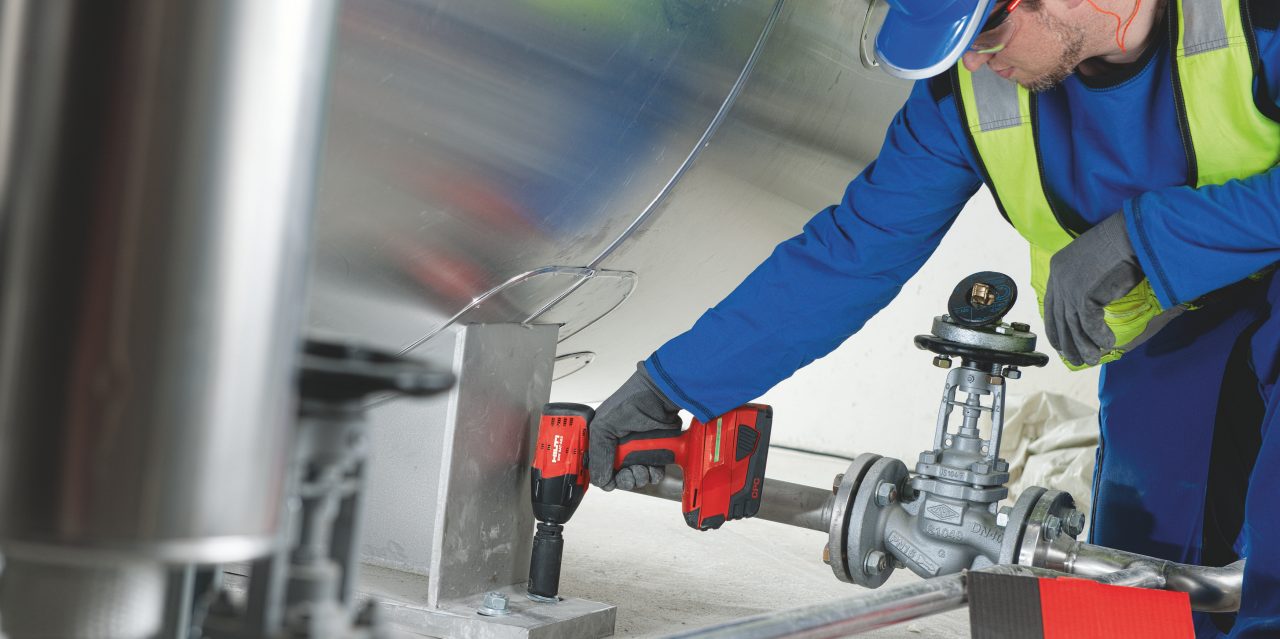
Installation and Torqueing
Reduce the amount of unplanned design work during the construction phase.
The AT system workflow meets the need for a high-productivity solution that can be delivered quickly and by any available worker.
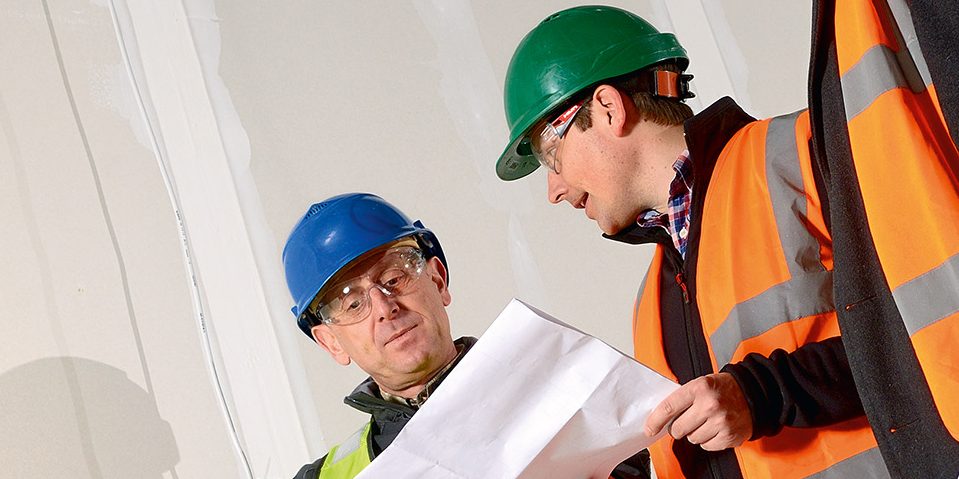
Site Inspection
The report generated by the AT System help you reduce time spend in installation inspections.
Results in a reduction of risk due to incorrectly torqued anchors and fewer opportunities for structural defects to emerge over time.
Easily generate your installation report
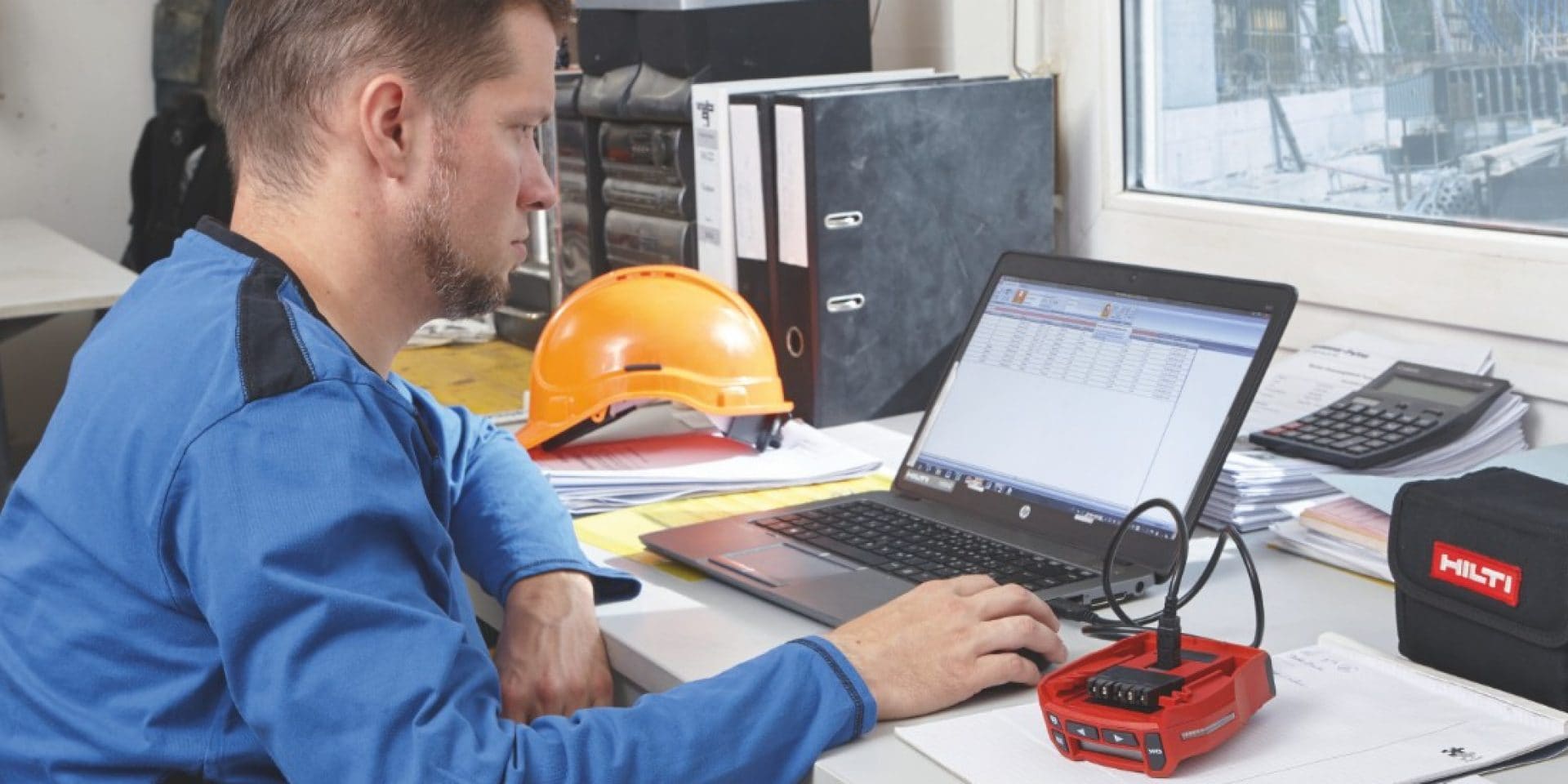
Full accountability has never been easier. The contractor or installer can simply connect the SI-AT-A22 module to a computer using a standard USB cable and the AT Documentation Software then downloads performance data stored by the SI-AT-A22, which can be used to produce an installation report.
The report lists all products used, the method of selection (scan or manual), completion time/date, and the type of action completed by the installer.
From a specifier’s perspective, this report proves that the anchors have been correctly torqued according to the instructions for use and meet certification requirements. From an installer’s point of view, it can help you breeze through site inspections.
Done right, the first time
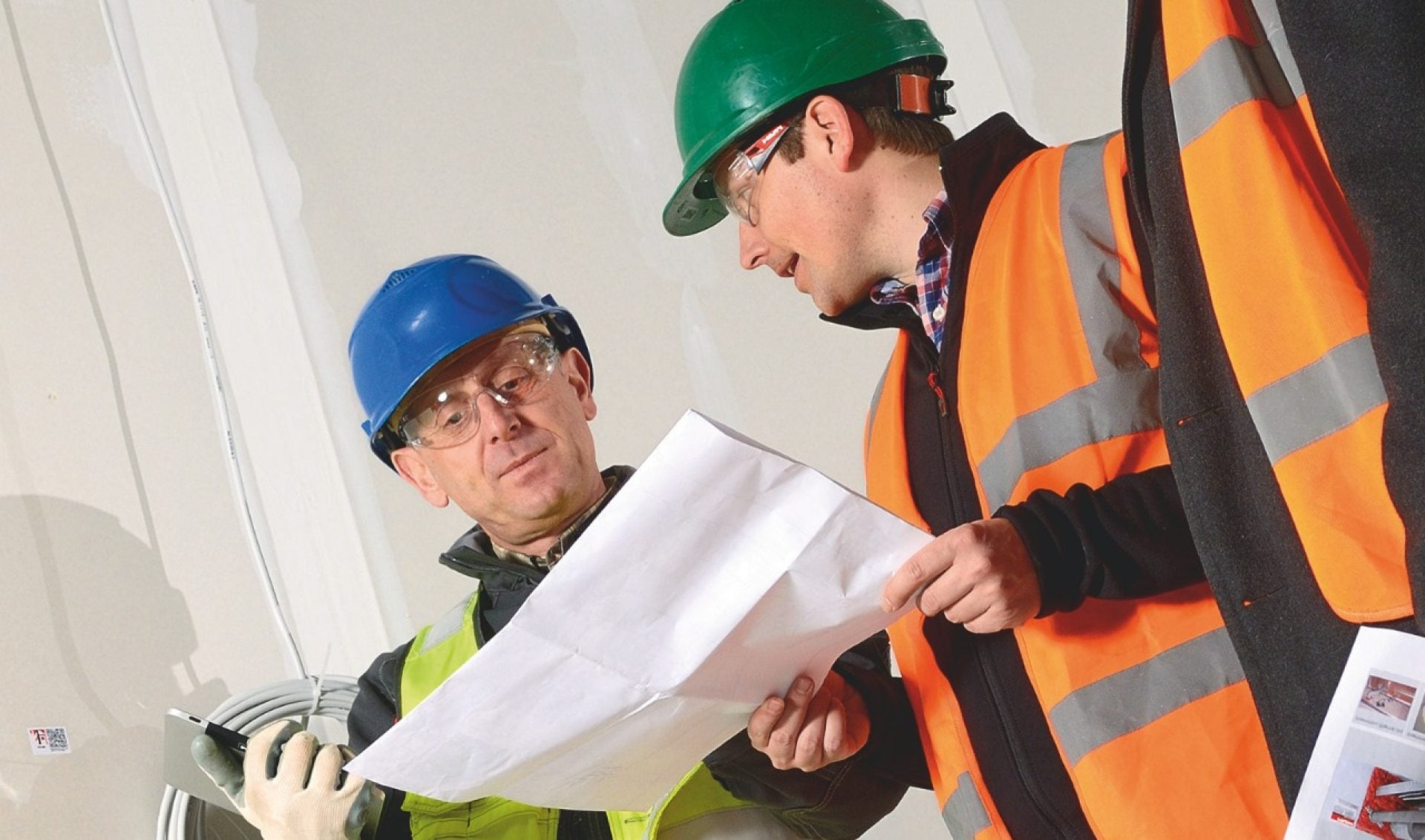
Quality control inspections are increasing on jobsites. There can be no doubt that these inspections are an important pillar of building safety, but they have their limitations. For example, routine inspections cannot detect all installation errors. Even the torque checks which are a standard component of most inspections cannot provide a conclusively show an anchor’s condition.
Surveys conducted with construction engineers have revealed that designers typically incorporate excessive safety factors into their design to ensure that they pass building inspections. Needless to say, this is not economical. Even with extra precautionary measures in place, inspections can still identify errors which demand additional re-working to correct.
Not time to waste on remedial work? Time to specify the AT system.
The anchor setting trifecta: SafeSet
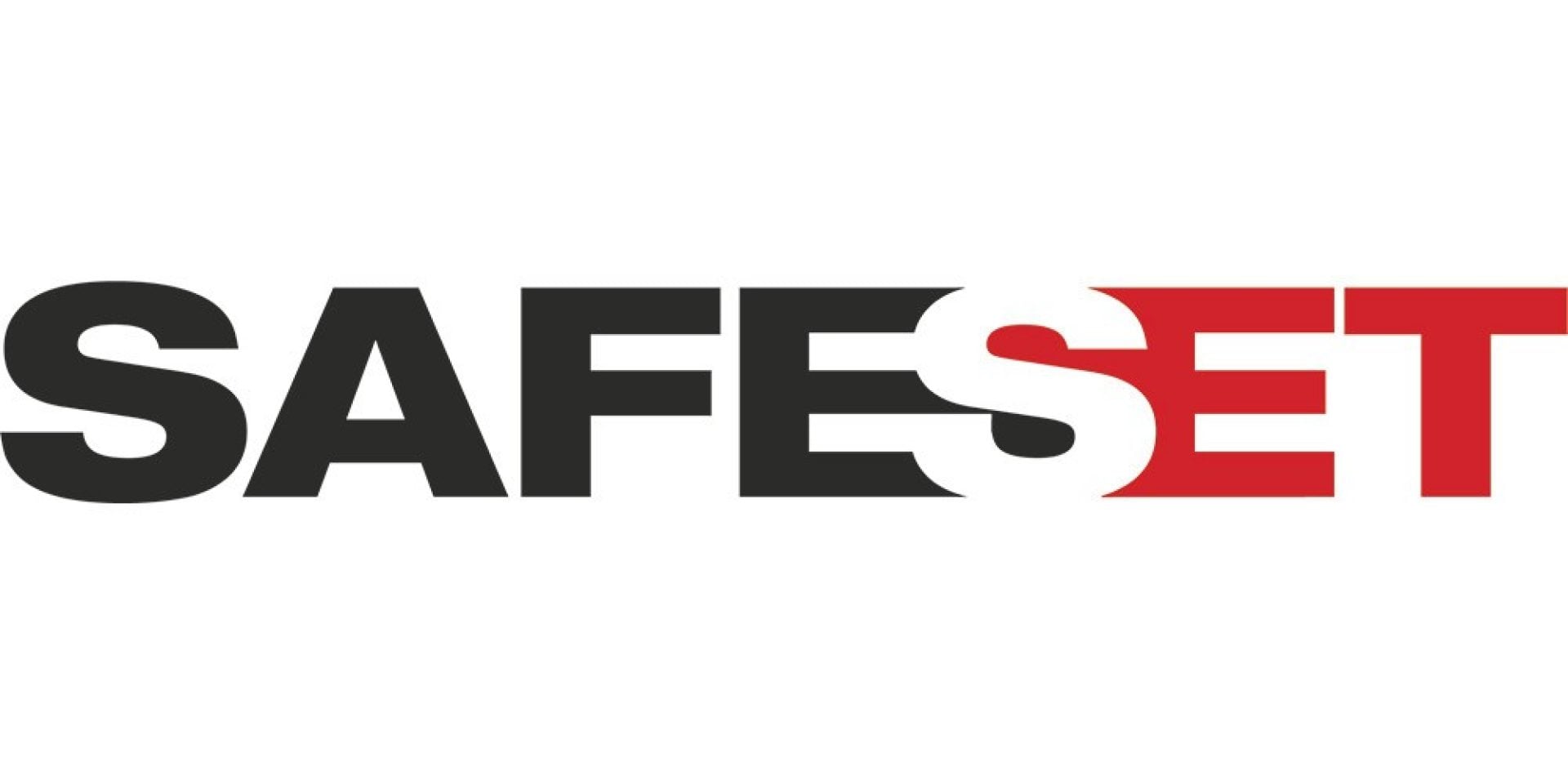
Safety. Productivity. Approval. SafeSet is Hilti’s proven methodology for consistently high-quality anchor installation at lightning speed.
The SIW 6AT-A22, along with the SI-AT-A22 module, fulfills all SafeSet criteria because they save time and reduce costs while also removing scope for installation error.